Cutting-edge roll stock transport marks another efficiency win for Acme Corrugated Box customers and processes.
Completed in late 2022, Acme Corrugated Box’s expansion added 80,000 square feet and a 50 percent manufacturing capability increase to the company’s Hatboro, Pennsylvania headquarters. Of course, expansion planning began years earlier.
In 2020, an internal five-person expansion team was assembled to lead decisions about equipment, supply partners, and other critical aspects of the build. In addition to increased space and capacity, the team aimed to put Acme Corrugated Box at the forefront of corrugated industry practices.
Kevin Landman, Corrugator Superintendent, was among the team’s appointed members.
“Our team traveled to box plants and equipment manufacturing facilities worldwide, assessing prospective equipment and partners through the lenses of several metrics including safety, quality, productivity, and waste,” Landman explains.
Productivity and safety in particular drove conversations about roll handling. Roll handling is the delivery of paper to corrugators on the box manufacturing floor, and an essential aspect of day-to-day operations. Up to that point, Acme Corrugated Box roll handling was carried out the traditional way: Clamp trucks driven by operators retrieved rolls of paper – called roll stock – from the roll storage area and delivered it to the wet end of the corrugator.
Beyond requiring manual labor, this age-old process put clamp trucks within a few feet of employees and equipment, risking injury and equipment damage. Efficiency suffered, too. Clamp truck operators’ attention was constantly divided between roll handling and other important responsibilities including roll stock inspection.
The Acme Corrugated Box expansion team eagerly explored emerging technologies for improving the roll handling process. They honed in on Harmax.
INTRODUCING HARMAX
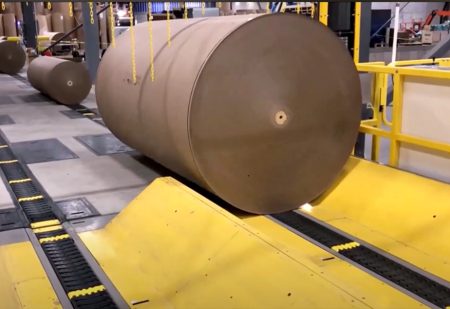
With more than 40 years of experience designing and manufacturing roll handling systems for industries including corrugated packaging, Harmax’s roll delivery system checked every box on Acme Corrugated Box’s list.
The system uses an in-ground conveyor measuring more than 100 feet in length to move paper to corrugators. Rolls of paper are dropped and transported automatically to the corrugator via the conveyor roll track and a transfer roll car.
The expansion team at Acme Corrugated Box immediately saw the system’s potential benefits for efficiency. Beyond eliminating the need for manual loading, trucks, and time spent driving back and forth, rolls for future jobs could be staged while awaiting transport to the corrugator. Freed from dropping rolls at the equipment, clamp truck operators could focus on roll inventory, unloading incoming roll stock, and roll stock inspection. The Harmax system also utilizes squaring sections and tracks that eliminate risk of damaged roll cores due to misalignment.
UP AND ROLLING
The Harmax roll delivery system was installed at Acme Corrugated Box’s newly-expanded Pennsylvania facility in December of 2021. Harmax programmers spent several days onsite calibrating the system, overseeing quality control testing, then training Acme Corrugated Box’s production team on how to run and maintain it.
It was commissioned into production in March of 2022 – and, as hoped, has taken Acme Corrugated Box’s manufacturing floor efficiency to new heights.
“The Harmax roll delivery system is a huge stride in Acme Corrugated Box’s quest to do more with less,” Landman says. “So much time is saved by eliminating the back and forth of driving from the roll room to the corrugator – time that truck operators now invest elsewhere. The system has gone a long way toward honoring our promise to handle Acme Corrugated Box customers’ ever-changing business needs more efficiently and more safely.” To see the roll delivery system in action, check out this video to discover how Acme Corrugated Box can support your evolving business needs.