A mindset as much as a methodology, Continuous Improvement has big benefits for customers and employees at Acme Corrugated Box.
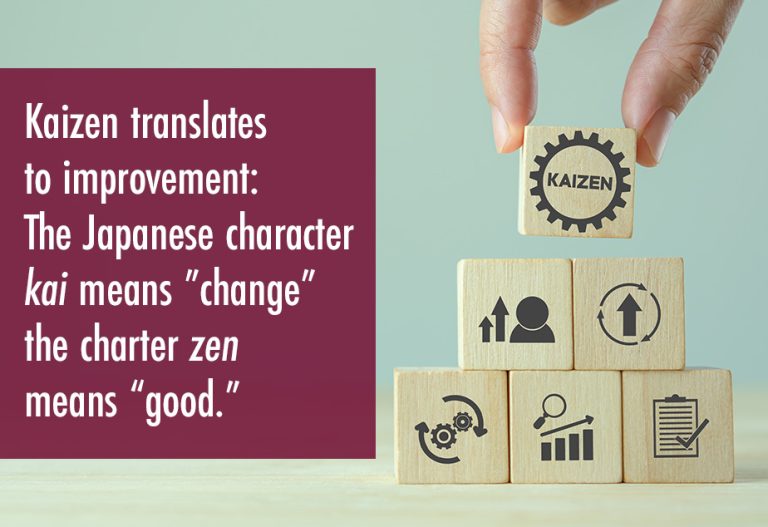
Floor markings guiding process flow. Shadow boards showing designated spots for each tool. An employee whose singular focus is ensuring efficient production runs.
At Acme Corrugated Box, these everyday measures all fall under Continuous Improvement. While most customers never see or hear about our Continuous Improvement department, it’s one of our company’s winning ingredients – and not commonly seen in our industry.
“Decreased downtime, shorter setup times, higher morale and retention – these are all fruits of Continuous Improvement here at Acme Corrugated Box,” says Alex Cohen, Operational Excellence Manager. “They’re passed to our customers in the form of box quality, cost, and on-time delivery. Honestly, I’m surprised more box manufacturers don’t adopt it.”
WHAT’S “CONTINUOUS IMPROVEMENT”?
Continuous Improvement is a rolling basis methodology that identifies problems impeding efficiency, then makes changes to fix them. Continuous improvement culture is widely attributed to Ford Motor Company, but as a formal business methodology, it began in Japan. In fact, the word Kaizen – the name of Continuous Improvement’s lead strategy – literally translates to improvement: The Japanese character kai means “change;” the character zen means “good.”
WHY CONTINUOUS IMPROVEMENT?
Companies with dedicated Continuous Improvement departments consistently outperform their counterparts in terms of longevity, customer satisfaction, and outcomes overall. This reality is what inspired Acme Corrugated Box to adopt the methodology more than ten years ago.
“Around 2010, we saw opportunity to tighten operations for a number of reasons, including the desire to keep cost down and drive quality up,” Cohen explains.
The Continuous Improvement department at Acme Corrugated Box was designed to address day-to-day problems faced by plant operators. As needed, events such as Kaizens – learning initiatives that typically last a week, – dig deep into the root causes of workplace hurdles and develop clear solutions. Recently, for example, Acme Corrugated Box hosted a small Kaizen event focused on glue issues some customers were experiencing, and worked to remedy the matter.
“Continuous Improvement generates solutions that benefit our customers and our teams. It’s a win-win,” Cohen says.
WHAT IT TAKES
While Continuous Improvement’s premise – ongoing change – sounds simple enough, Cohen notes that adoption of the methodology really does require a company-wide mindset shift.
“Change is sometimes seen as a dirty word in business,” he says. “For Continuous Improvement to work, change needs to be seen as a good thing, which requires an initial shift in thinking for many employees.”
Thanks to successful Continuous Improvement adoption over the last decade, today Acme Corrugated Box employees at every level routinely seek ways to reduce wasted time, material, and energy.
“We use the acronym D.O.W.N.T.I.M.E to remind us of what might be impeding efficiency – that is, Defects, Overproduction, Waiting, Not utilizing talent, Transportation, Inventory excess, Motion, and/or Excess processing,” Cohen explains.
In terms of company structure, Acme Corrugated Box’s Continuous Improvement department works hand-in-hand with the Quality Assurance Department. Both fall under the umbrella of Operational Excellence.
“While Continuous Improvement is focused primarily on run efficiencies, Quality Assurance is focused on creating a good product and getting it to end users every time,” Cohen says. “It’s yet another winning combination. Together, these departments ensure the best possible product, and the best possible process for creating it.”
Want to take advantage of high-quality products created by Acme Corrugated Box’s Continuous Improvement initiatives – or become part of our trusted team? Please visit us at acmebox.com.